Alumina catalyst carrier is one kind of catalyst carrier (other name catalyst support) It have two formed: a white powder or formed alumina solid.
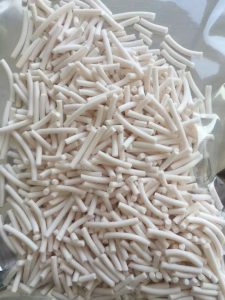
what is the catalyst support?
Alumina catalyst carrier application range
Alumina catalyst carrier is the most widely used catalyst carrier, accounting for about 70% of the industrially supported catalyst.
There are many forms of alumina catalyst carrier, not only different forms of different nature, even though the same form also because of their different sources, but have different properties, such as density, pore structure, specific surface area.These properties have important implications for the alumina used as a catalyst support. Alumina is mostly prepared from its hydroxide (also known as hydrated alumina or alumina hydrate).
Alumina catalyst morphology structure
Commercial alumina carriers are powdered, but most are already shaped.
Strips, spheres, and ingots are mostly used as supports for catalysts in fixed-bed reactors, and microspheroidal alumina supports are mostly used in fluidized-bed reactors.
It is also possible to make shaped supports required for specific catalysis processes, such as rings, trilobes, honeycombs, fibrils (see alumina fibers) and the like. Apart from solids, there is an alumina sol for sale.
Important parameters when choosing alumina are crystal form, purity, specific surface area, pore structure and bulk density. The specific surface area of α-alumina is very low (less than 1 m 2 / g), and the specific surface area of the transition alumina is generally 10 to 102 m 2 / g. The formed commercial alumina supports are mostly porous materials. The pore size and distribution have an important influence on the diffusion properties of the reactants in the catalyst particles during the catalytic process. Pore pore size can be less than 20 ┱, coarse pores up to the micron-level pore structure varies with species.
All transitional aluminas contain more or less water, with some hydroxyl groups and exposed aluminum atoms on the surface, exhibiting the characteristics of B and L acids (see Acid-Base Catalyst) Nature has important implications. Surface acidity and preparation conditions, especially with the impurity ions and heat treatment temperature. Negative ions such as halogens enhance the surface acidity of the alumina, and the enhanced acidity will promote the catalytic function of the alumina itself on the cracking and isomerization reactions of hydrocarbons.
Alumina catalyst carrier usage
-
load catalytically active components.
Alumina with a small specific surface area (or a material with only a small amount of coarse pores) is generally used for supporting catalyst active components having a high specific activity. With such carriers can eliminate the diffusion effect in the pores, in the selective oxidation process for the purpose, can reduce the depth of oxidation side reactions. Such as ethylene oxide to silver oxide catalyst used to that of α-alumina as a carrier. Alumina with a large specific surface area has well-developed pore structure, which enables highly dispersed active components of the catalyst to be dispersed into fine particles and prevents the active component particles from sintering and sintering during use by the barrier function of the support, which is a wide range The alumina carrier used. For example, precious metal palladium, platinum, rhodium and the like are dispersed on an alumina carrier to form a hydrogenation catalyst, which can improve the utilization rate of precious metals.
-
The surface acidity of the alumina and the supported active components constitute a bifunctional catalyst.
Such as the use of platinum in platinum reforming – alumina catalyst, which both as a carrier of alumina and catalyst active component. In some cases there is a strong interaction between the alumina support and a highly dispersive metal, such as platinum, which can affect the catalytic properties of the metal.